Vallourec delivers the first 3D printed metal parts to the Brazilian OCTG market


From now on, supply chain agility and delivery time efficiency reach a new level. With the use of WAAM (Wire Arc Additive Manufacturing) technology by the Vallourec Research Center, additive manufacturing or 3D printing has become a faster option for producing metallic parts and accessories to meet specific customer applications.
In Brazil, the first 3D-printed metallic accessories – four Test Caps – were delivered by Vallourec to a service company for use in an offshore exploration field.
“The customer requested a very challenging deadline for the delivery of the accessories. It was possible to produce them in approximately two months using WAAM technology, while the conventional lead time for manufacturing ranges from four to six months, depending on the availability of raw materials. We found that 3D printing would be an excellent alternative after consulting with our specialists, as it would guarantee delivery in the shortest lead time with the same level of quality within the customer's technical specifications and regulatory items", explains Laísa Rigueti, Innovation analyst from Vallourec.
Final quality is the same as in the conventional manufacturing process
With the guarantee that the accessory would meet all the specifications, just like one produced by the conventional process, the customer did not identify any technical problem in having the parts manufactured by this method, thus taking advantage of the opportunity of being the first in Brazil to use the 3D printed accessories.
Despite being simple design parts, accessories such as Test Caps must be produced project by project, due to the different dimensional combinations, metallurgy and type of connection. Test Caps are used to seal a production column and allow a hydrostatic test to be carried out on the well.
The four accessories, with two different dimensional specifications, were produced in microalloyed carbon steel, heat treated and inspected by ultrasound.
“WAAM uses an electric arc controlled by a robotic arm to fuse the wire directly to the surface of the base, or part, layer by layer. This technology has great flexibility and can build even shapes that are not possible with traditional methods, using metallic materials”, adds Ronaldo Antunes, R&D engineer at Vallourec.
Globally, lifting accessories, sealing rings and recirculation heads have already been produced with this additive manufacturing technology, all with satisfactory performance.
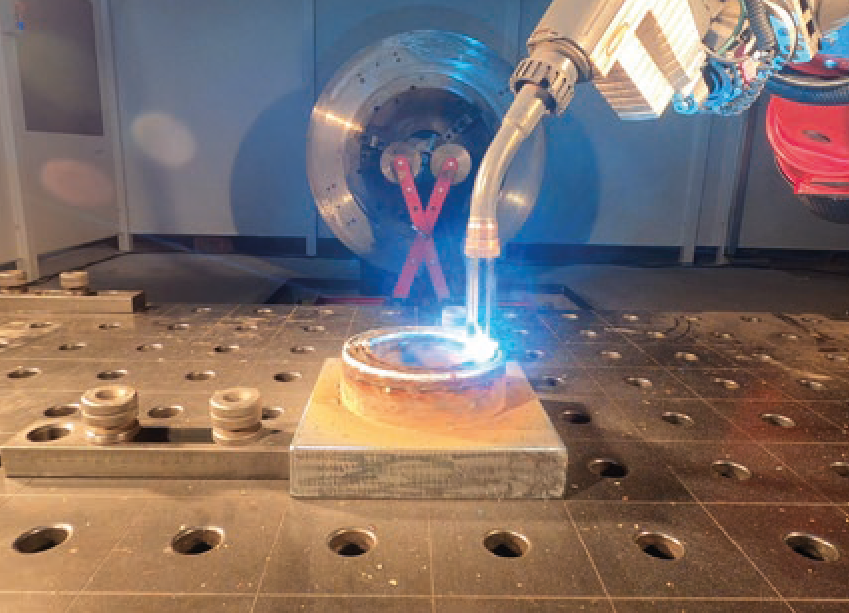
Flexible technology
In addition to serving the OCTG market, among others, WAAM technology can be used to manufacture parts for internal demands. With highly flexible, state-of-the-art equipment, much of the inventory will become virtual rather than physical.
“It’s much more feasible to have a database of manufacturing programs than to have physical parts in stock. For maintenance purposes, it is not feasible to have all the parts that make up a piece of equipment in stock”, says Gabriel Machado, technical salesman at Vallourec.
With the possibility of using WAAM technology to print a single piece, for immediate use or stock replacement, predictive and preventive maintenance actions gain much more agility, with lower cost. From the moment the possibility of failure is detected, the part can be manufactured more quickly, guaranteeing the reliability and continuity of operation of the equipment.
“This is a strategy that is being evaluated for internal use”, emphasizes Gabriel.
“We have already heard from customers who have robust inventories to prevent critical stops that they discovered, at the time of use, that the parts in stock, even repeated ones, were non-compliant. So, they had to wait for long delivery times, which will change drastically with the flexibility of WAAM, which can make an identical part, or a provisional one, or even a part with improvements, in a matter of days”, recalls Ronaldo Antunes.

Next steps
For the time being, a printing cell is available at Vallourec’s facilities in Singapore, one in Germany and two in France, developing new products in the Additive Manufacturing Competence Centers, or producing parts and accessories in these Production Centers, which have been shipped to plants worldwide for qualification or regular use.
“We are in the market validation phase, but the idea is that, based on the increase in demand, new cells will be installed in other regions. Right here we already have new applications and projects under analysis. This is a market that demands many pieces of complex dimensions and shapes, whose manufacturing process is slow and expensive. With WAAM, it is possible to have a more aggressive lead time and costs, with a much simpler production”, emphasizes Laísa.
And, going even further in the delivery of ease and agility, the “Vallourec Additive Manufacturing” app is in the testing phase, which will allow the customer to enter their specifications directly on the mobile interface. The application creates a 3D image and a digital file from the data that will be used for 3D printing.
The app helps determine specific needs and whether the project is viable using additive manufacturing. It also provides an estimated timeline and cost for the product, depending on whether the part is already part of Vallourec’s database or needs to be prototyped, tested and qualified.
For the next step, the app development team plans to add even more functionality. After completion of the part and schedule, the file will be delivered in digital format, and the customer will be able to access it and obtain a printout of the product close to their workplace.